房车不同于家用轿车,房车进入中国的时间并不长,房车市场也还处于起步阶段。而在生产制造方面,相比国内汽车工厂的高度自动化、电子化及智能化,国内大部分房车工厂还处于改装厂的阶段;对比汽车工厂内先进的自动化装配机器人、3D打印零配件甚至是装备机械外骨骼的工人,部分房车工厂的现状可能是搬运基本靠手、通讯基本靠吼。然而在江苏溧阳,却有着一个开挂般的存在,那就是上汽大通溧阳房车生产基地。
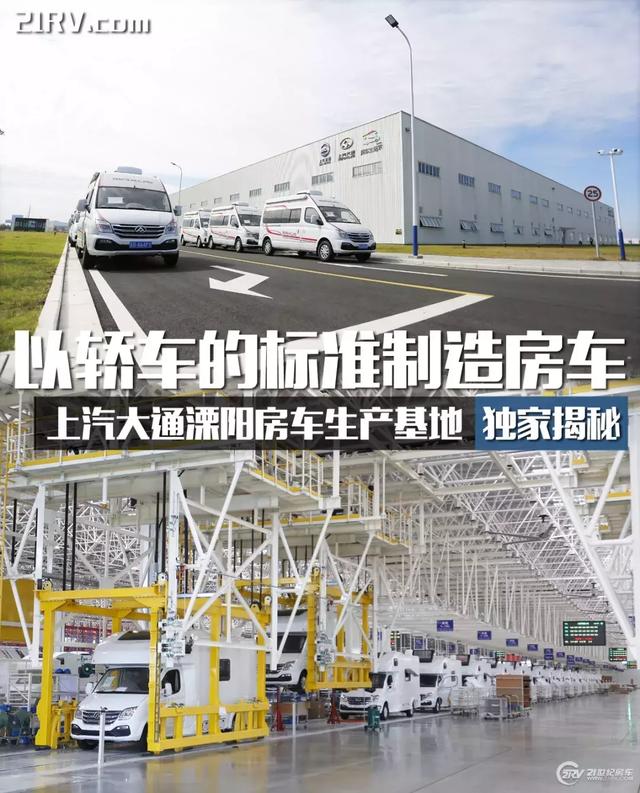
上汽大通溧阳房车生产基地由上汽大通房车科技有限公司投资建设,一期占地面积420亩,总投资金额超6亿元。上汽大通溧阳房车生产基地是国内最大的也是首个专为定制化房车打造的研发及生产基地,可实现多平台产品共线生产,包含RV80 B型/C型、营地拖挂RT11及RG10等车型。值得一提的是,溧阳房车生产基地是国内第一家能够与基型车同步开发的房车工厂,也是第一家完全引入整车开发流程的房车企业,国内第一个实现批量化C2B产品开发的房车企业。
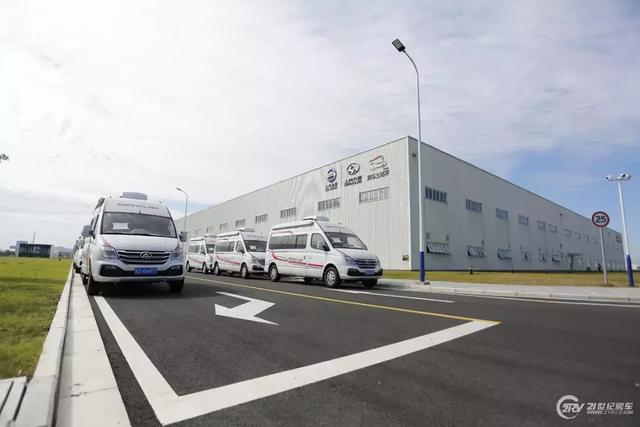
溧阳房车生产基地总面积达420亩,主要分为工厂生产区域、研发展示中心及房车生态体验区三部分;此次我们为大家重点揭秘的就是溧阳房车生产基地的工厂区域,目前一期制造车间44860平米,工厂于2017年3月开始奠基,10月份竣工并进行试生产,2018年1月正式投入生产。
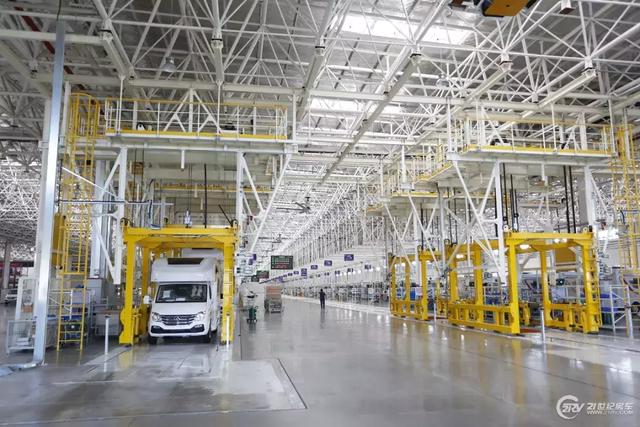
刚进入工厂内部,眼前的景象确实令我有些意外,首先映入眼帘的是两条全自动房车装配生产线,每条生产线共有21个工位,全长约210米,是国内目前最长的两条房车生产线,从2018年1月开始投产至今已经累计生产超2000台房车。
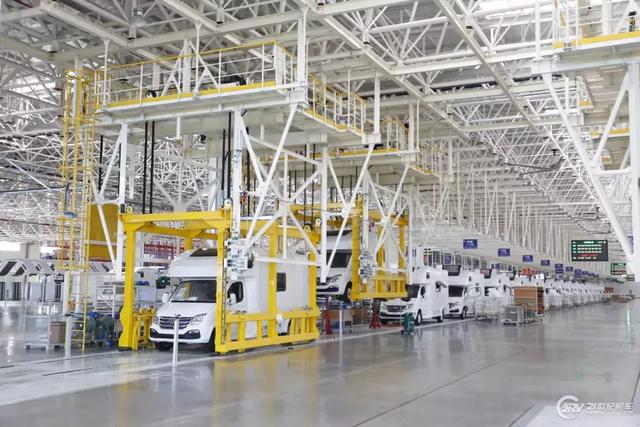
工厂内最引人注意的就是这条中国最长的全自动房车生产流水线,制造车间对标国外Hobby、Hymer等一流房车工厂的技术标准。车间引进欧洲先进的生产设备,建设柔性化装配车间、智能化家具车间、厢板车间及自动化智能物流配送系统,设备先进程度处于行业领先位置。
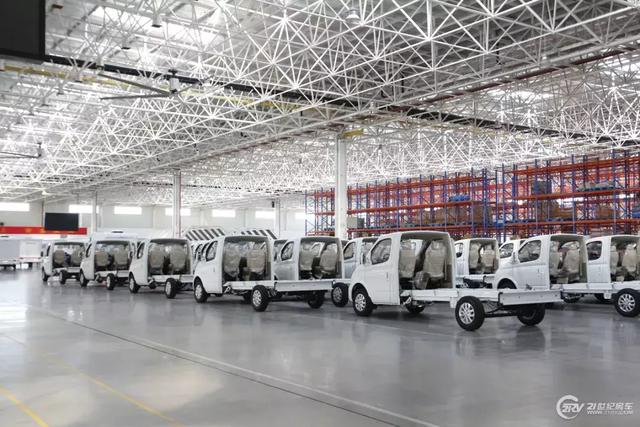
上图为工厂内用来临时存放自行式C型房车底盘的区域,用以打造上汽大通房车旗下的RV80车型。
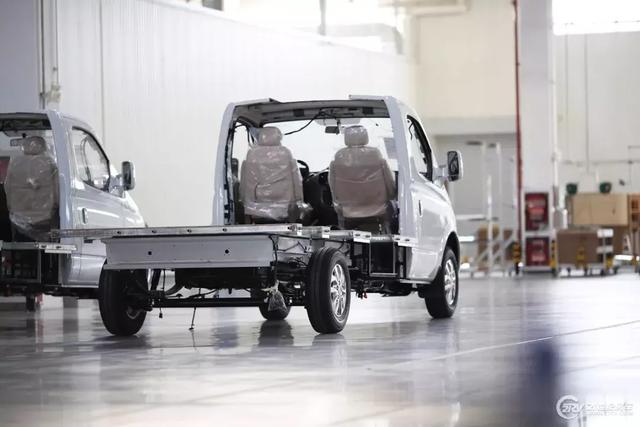
对于有着乘用车研发制造背景的上汽大通房车来说,用于制造自行式房车的底盘均经过严谨完善的底盘耐久试验及翻滚试验等,从而确保上汽大通房车的耐用及安全性,这种上汽大通房车特有的技术优势是原厂品质的基础保证。
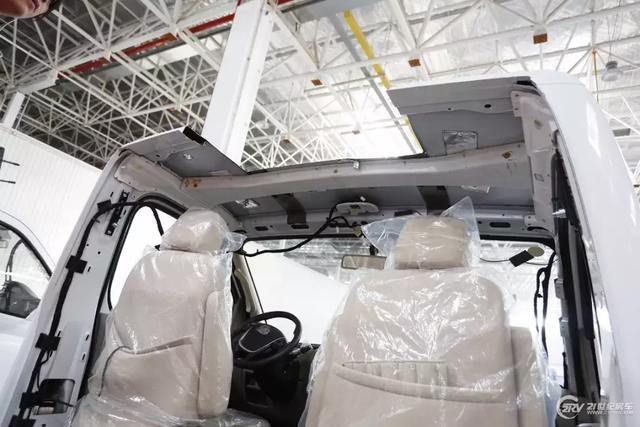
在此前我曾对上汽大通房车配备的车载电视尺寸提出过疑问,在大家都争相使用大尺寸电视时,为何上汽大通房车偏偏不讨巧地采用一款尺寸偏小的电视。而上汽大通房车的研发人员是这样回答我的:“驾驶室强度直接决定了乘客安全性,对于C型房车来说,驾驶室顶部需要切割开口安装车载电视。实际上我们也知道大尺寸电视对消费者有着更强的吸引力,但在初期设计时,由于对驾驶室整体刚度的考虑,驾驶室A柱、B柱,驾驶室顶横梁及前顶横梁组成了一个能够在车辆发生碰撞时保证乘客安全的骨架结构;我们在经过严谨的理论计算及电脑虚拟仿真分析后,确定了驾驶室顶部的最佳开口尺寸,在后期还进行了25000公里的实车测试,从而验证我们的房车驾驶室在发生碰撞时能够保证乘客的安全,另外在长期行驶中也不会发生变形。”
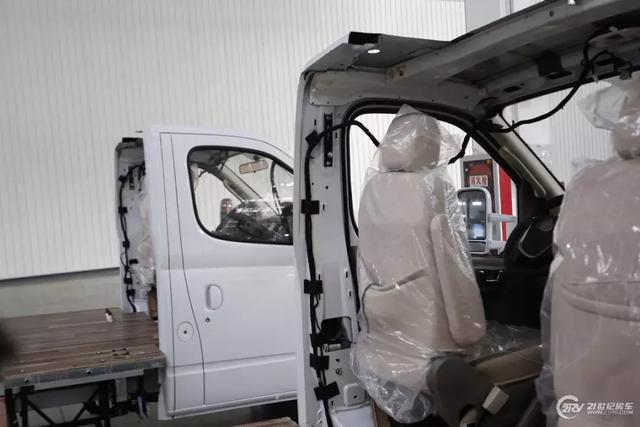
上汽大通房车底盘的B柱部分也同时进行了加强,在腔体内填充了大量加强材料来增加B柱刚性,从而全面提升驾驶室的安全性。
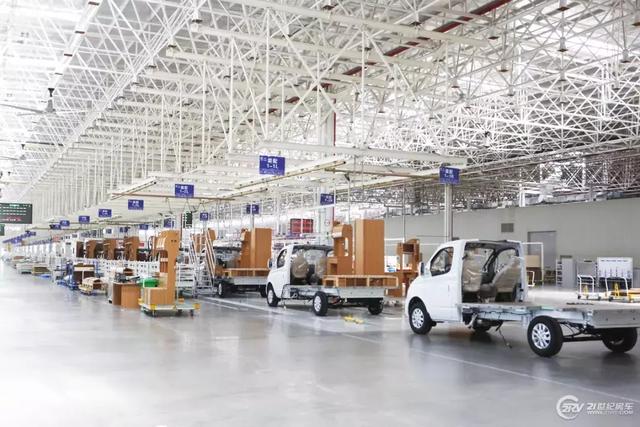
相对于国内很多房车厂商,上汽大通在房车制造工艺上,采用了先进的由内至外装配工艺。虽然由外到内与由内到外听起来像是一个很简单的变化,实则改变了整个产品的工艺路径,关系重大。对于由外而内的装配工艺来说,在合拼箱板后再安装家具,由于无法避免的安装公差,有很大几率使得家具的连接零件出现轻微变形从而产生内应力。而零件与零件之间的内应力会始终存在,就好似一颗定时炸弹,行驶在颠簸路段时很有可能通过震动将内应力释放,从而造成零件的松动、异响甚至脱落。所以在房车设计过程中,应尽可能避免内应力的产生。而上汽大通所采用的由内而外的生产工艺,所有的家具都不依靠箱板进行安装定位,独立成为受力结构,能够很好地避免零件之间内应力。
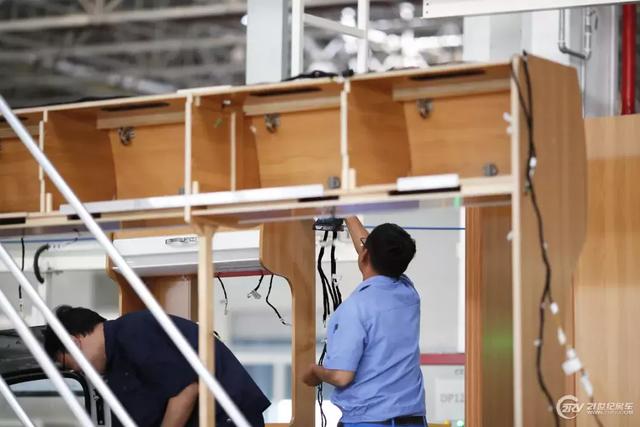
除此之外,由内而外的装配工艺形成了开放式工作环境,同一工位可同时容纳多名工人进行装配,工作效率更高;另外一方面就是有利于通风,当房车交付到客户手中时,车内空气质量已经处于一个稳定而良好的水平。

生产线的每一个工位上均带有标号,从1-21号工位覆盖整个房车装配流程,最后进入质检环节。
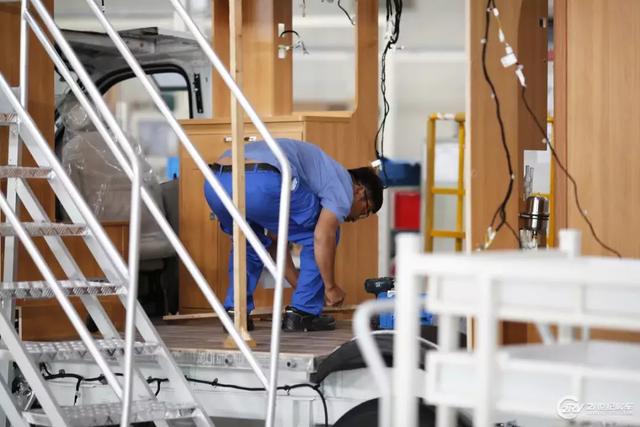
在房车地板部分,上汽大通房车较为保守地选用了更加耐冲击的钢骨架地板,而非像欧洲房车那样采用轻质地板,这也是出于对中国路况条件考虑。在质量控制方面,生产线对于房车地板的平整度也有着完善严格的监测标准。
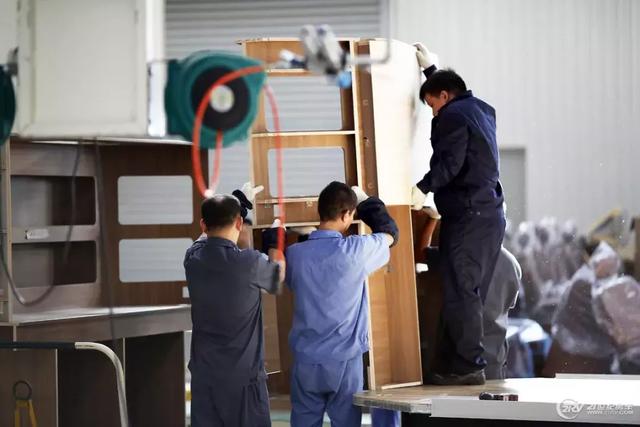
参观生产线时我发现,上汽大通房车的家具装配已经实现了模块化安装,车间工人在家具装配区提前将板材、柜门及相应线束组装完成,从而在相应工位通过吊具直接将模块化家具在房车上进行定位及安装。这种模块化安装工艺不仅提高了装配质量及匹配精度,也极大提升了生产效率。

在家具存储区我们能看到大量的模块化家具,包括床架、储物柜及厨房整体结构等。值得一提的是,在生产流程标准化的同时,上汽大通房车还支持个性化定制,消费者可自由选择家具板材的款式配色等。
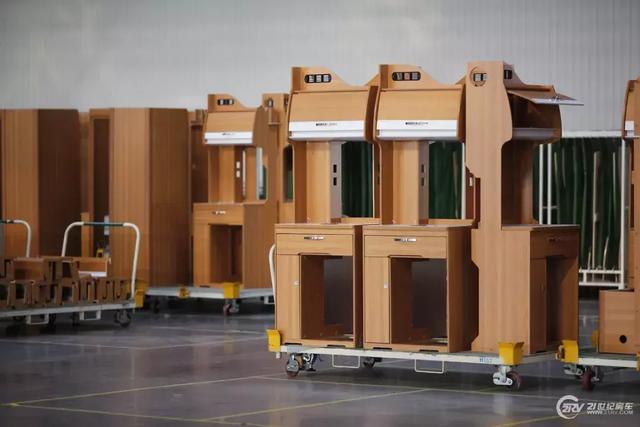
在车内空气质量控制方面,所有面向房车室内的零件均严格禁用不饱和树脂,在有效的降低车身重量、提升车身刚度的同时,极大的降低了各类挥发性有机物的含量,提升车内空气质量。车内空气质量的第二个主要污染源就是各类胶黏剂,不合格或者非车规的胶黏剂在车内高温、高湿等环境下,会持续的释放各种醛类物质,严重危害车内乘员健康;大通房车全部采用经过上汽集团严格认证的各类车用胶黏剂,满足乘用车、商用车的室内空气质量控制要求,在保证粘接效果的同时还可以大大降低各类有害气体。第三类影响房车空气质量的就是各类家具板材,上汽大通房车严格选择符合E0排放要求的板材,降低各类家具的挥发性有机物排放,通过前期多项措施整体提升上汽大通房车的车内空气质量。
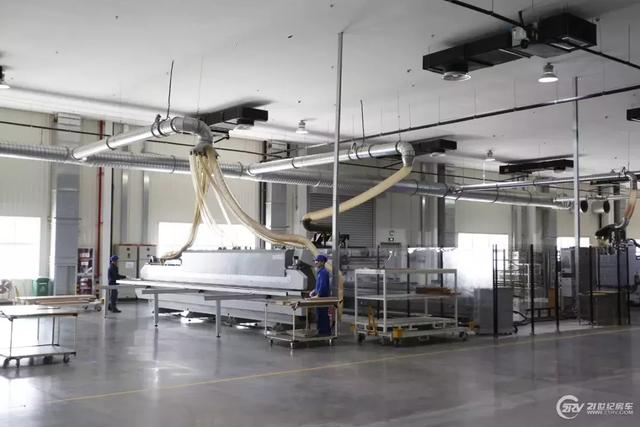
不同于大部分房车厂家,上汽大通房车没有选择对外采购家具,而是在生产基地中建设了独立的木工车间,从源头把控产品质量。家具制造区引进了世界排名前列的意大利Biesse和德国Homag的木工机械设备,软件上结合智能制造系统,大大提高板材加工制造效率。在木工车间里,房车家具的加工共分为三个环节,首先根据家具设计将板材切割成需要的形状,随后对板材进行封边;值得一提的是,工厂使用的封边机器能够对圆弧板及异型版进行自动封边。最后环节则是通过工人对家具板材进行打孔处理。而在明年下半年木工车间还计划进行二期的投产,二期将引进实木加工设备、自动覆膜机等新设备来实现更多元化的产品需求;除去提升常规板式家具产能,还会考虑美式拖挂房车的实木家具制造。
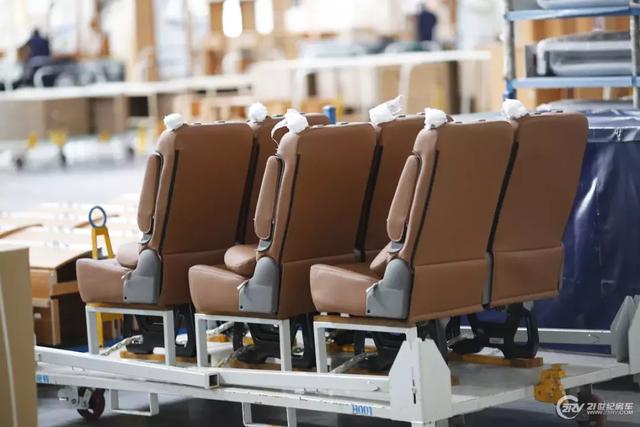
车内家具值得一提的还有座椅部分,大通房车科技有限公司的房车座椅是在大通原厂座椅的基础上针对房车特殊需求专门开发而成,具备头枕分级调节、靠背可向前向后调节、同时配置有扶手,乘客多环境使用均可调节到舒适的位置。另外座骨架及靠背骨架均有S型弹簧,行车过程中乘坐也有良好的减震功能。安全方面,后排座椅配置有三点式安全带,配置有不少于2个儿童安全座椅接口,给所有乘客安全保障;

车内座椅通过各项严苛试验,在强度、耐久性及舒适性等方面均有所保障。座椅蒙皮采用棕色PVC面料,具有无气电脑味,耐老化,易清洁等优点。
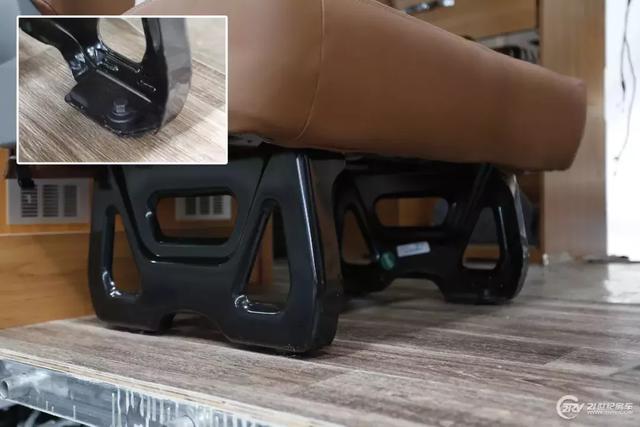
座椅可以说是房车内的核心安全配置,上汽大通房车座椅通过高强度等级螺栓和钢制底盘连接固定,在紧固螺栓时,扭矩经过严格标定,在工人完成紧固进行自检后,巡检员还会进行复检,在房车下线后还进行最终质检。对于所有关键路径上的标准件安装,至少有三道检验程序,从而确保整车安全符合乘用车安全标准。实际上在产品初期设计时,会锁定一些安全要素较高的零部件作为重点关注对象,从开发的前期到后期都会持续关注。
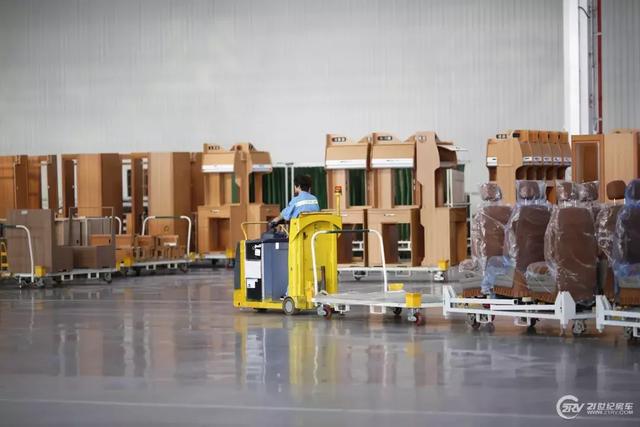
加工完成的车内家具会统一移至家具储存区存放,在工厂内随处可见工人驾驶着电动拖车搬运家具。
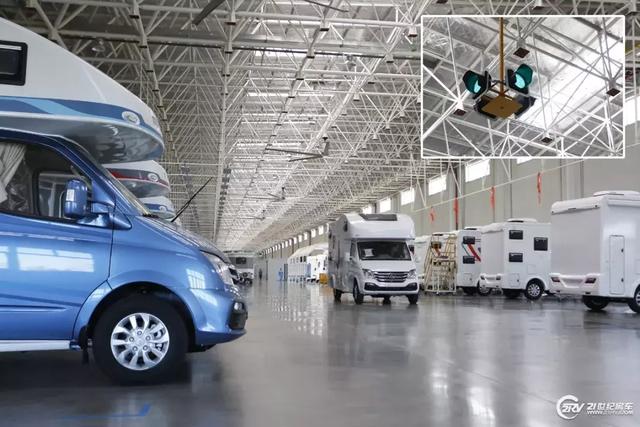
工厂内除去各类电动拖车、还有即将下线的房车在质检区域行驶,而工厂电脑在设计时也考虑周到,在一些转弯及路口处安装有交通信号灯,从而实现工厂内各种车辆的有序行驶,在提高生产效率的同时保证安全。
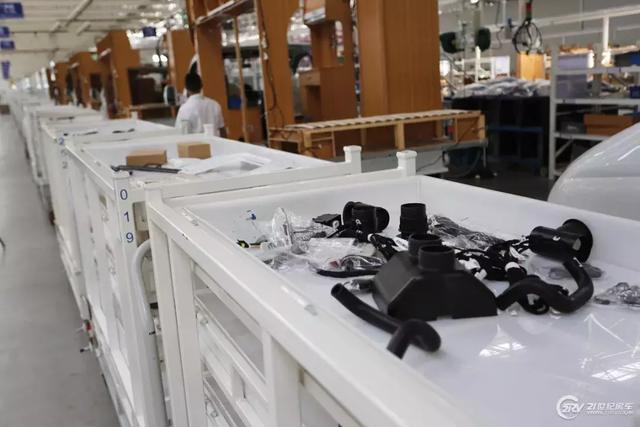
靠近工厂生产线会发现,在每个工位外侧的物料架上都备有该工位所需的零配件,从而提高工人的装配效率。
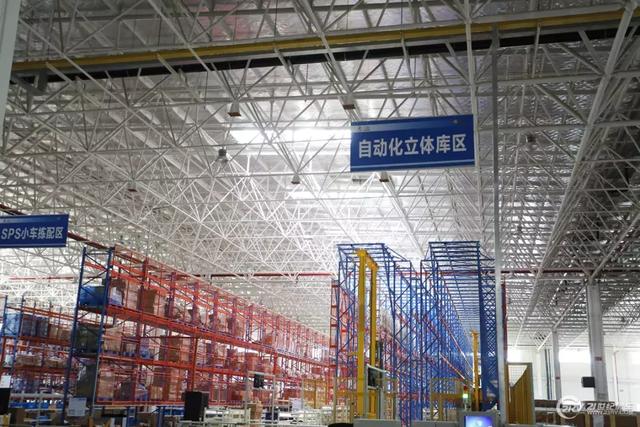
生产线上所需零件全部来自工厂的物料存储区域,针对房车定制化程度较高这一特点,在沿用乘用车物流工艺的同时,采用行业领先的AGC自动托运系统和配套SPS输送系统,大大增加了物料的配送速度,对生产效率的提高起到关键作用。走进物料储存区,从工厂顶部标牌可看出该区域主要分为自动化立体库区及SPS小车拣配区。
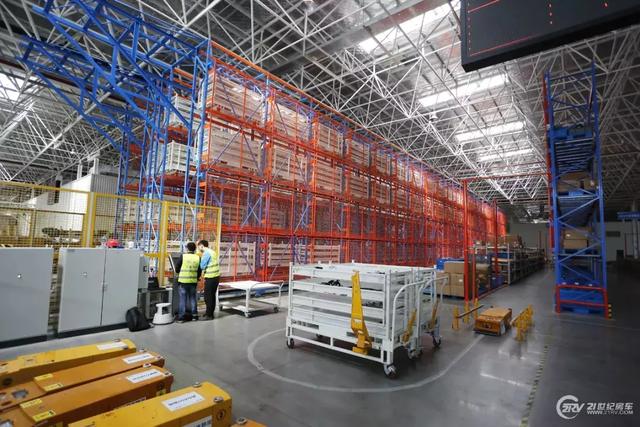
自动化立体库区域在设计时以满足工厂三天生产所需物料为基础,根据每款房车配电脑置表,每件物料都会生成专属条码,从而实现物料的有序存放。
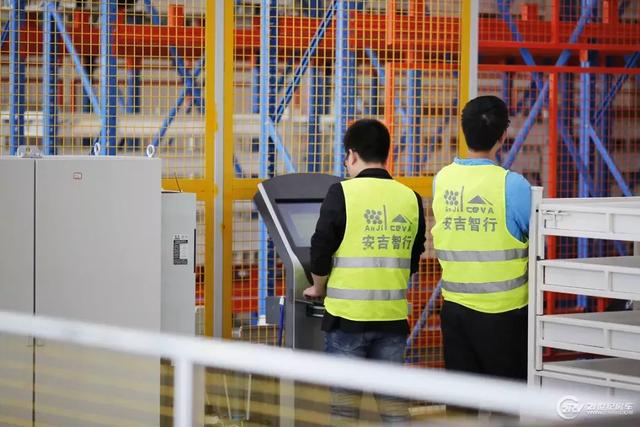
当需要物料出库时,工人通过操作台即可快速找到所需物料,随后可通过自动化设备将物料移动出库。
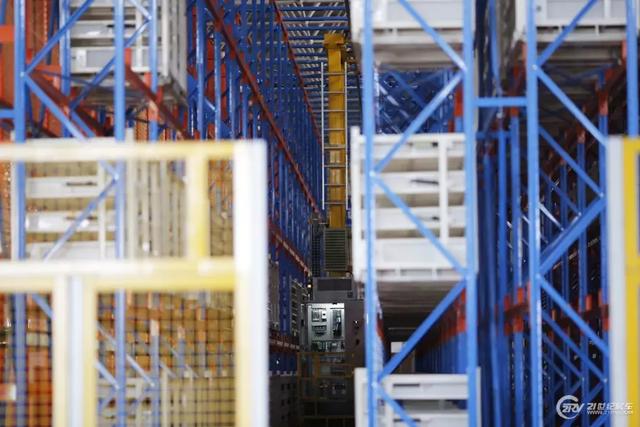
在自动化立体库每个货架间均设有轨道,从而实现了精准快速的物料出库。
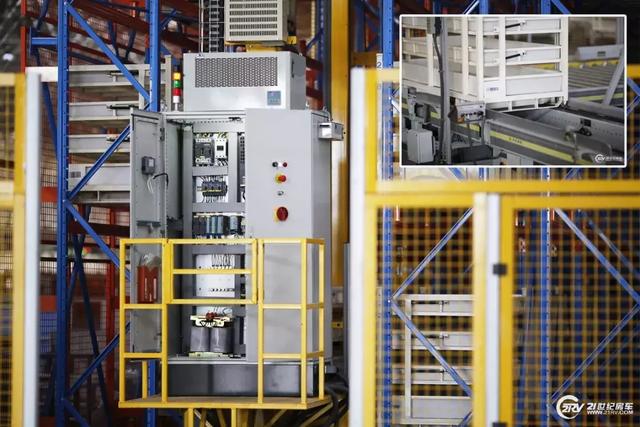
在自动化设备到达物料对应位置后,会自动从货架上提取物料,随后完成物料出库。
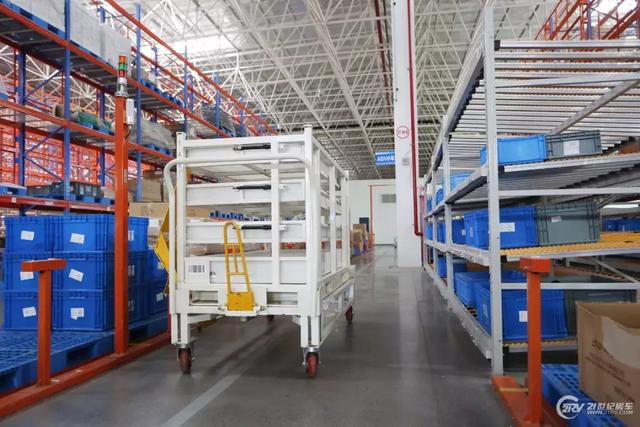
为了满足房车的个性化定制这一特点,在自动化立体库区旁还配套有SPS分拣系统,通过扫描条码而确定不同车型配置对应配件。
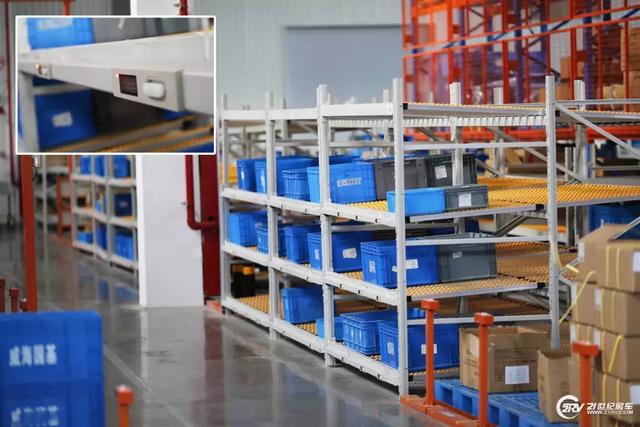
当车型配置确定后,配件架上的红色指示灯会转为绿色,工人可根据指示灯快速确定该车型所需配件,从而避免人为挑选物料可能出现的错误。
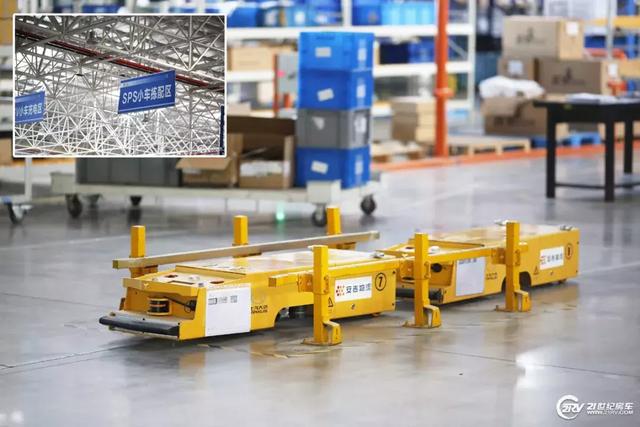
SPS物料系统是溧阳房车生产基地的一大亮点,也在一定程度上反映了工厂的自动化水平,在物料存储区随处可见的AGC小车担负着快速输送物料的使命。据工作人员介绍,每台AGC小车都价格不菲,造价基本相当于一台家用轿车。
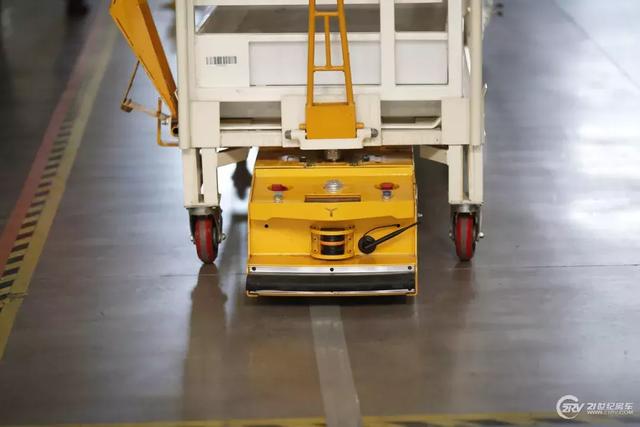
当SPS分拣系统根据配置信息完成了配件的分拣,AGC小车会自行前往分拣区与物料架结合。
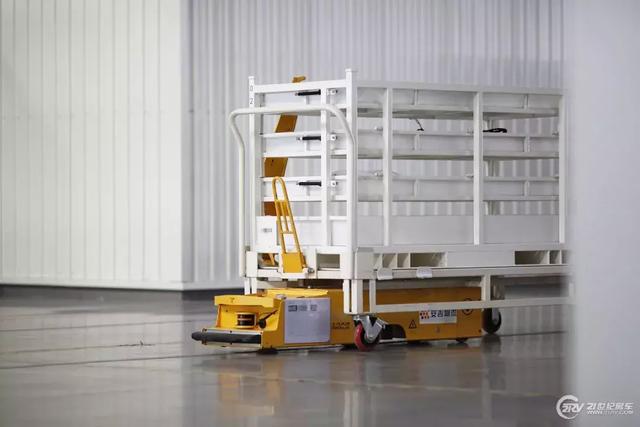
随后AGC小车会拖动已经装好配件的货架按照预设路线导航,在工厂内自动行驶。

最终AGC小车会携带所需物料精准快速地到达生产线对应工位,保证装配工人高效完成工作。
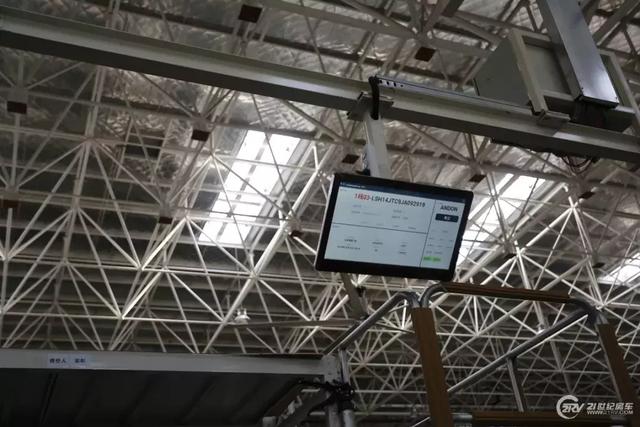
上汽大通房车还专门针对房车定制化程度较高这一特点为生产线开发了电子化装配指导书,通过条码编号自动识别房车配置,可显示车辆编号、车型及电子装配单,房车选配信息通过表格的形式直接显示在电子屏幕内。该系统集成于工位上方的触控屏内,除了起到安装指导功能外,当工人发现物料不足时,还可直接通过触控屏输入相应零件编号及所需数量,从而及时反馈给物料存储区进行物料补充;另外在装配出现问题时可通过触控屏呼叫班组长,设备故障时还可及时呼叫维修工进行快速返修。上汽大通溧阳房车生产基地的智能化不仅体现在物料运输上,生产线各环节智能化器件的应用也极大地提高了生产效率和生产品质。
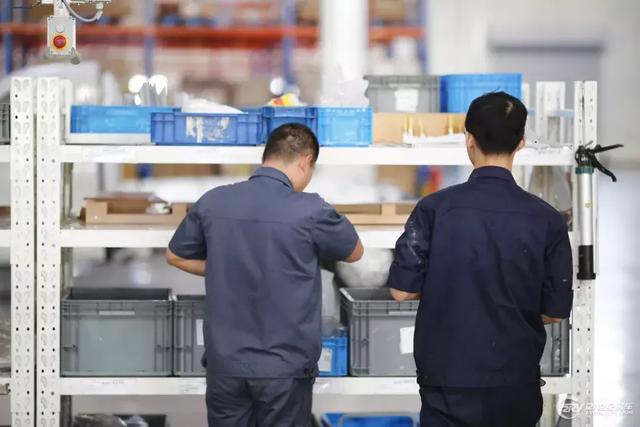
通过工位上方的电子化装配指导书,工人可快速挑选所需配件,不仅提高了工作效率,还很大程度避免了配件的错装及漏装。
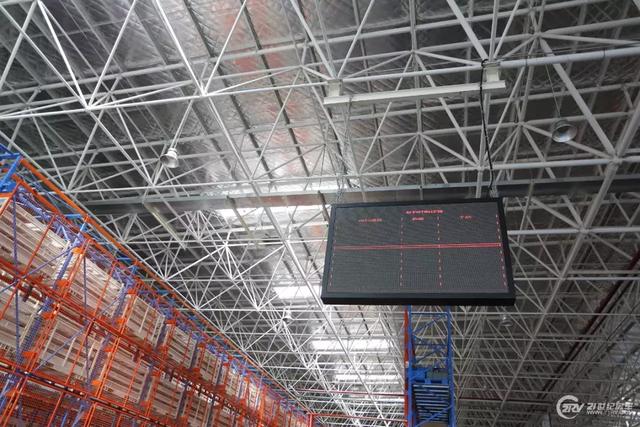
在物料存储区的醒目位置安装有一块大屏幕,当某个工位因缺少物料而进行呼叫时,屏幕上会及时显示所需物料编号、数量及对应工位,从而保证物料储存区工人快速响应。
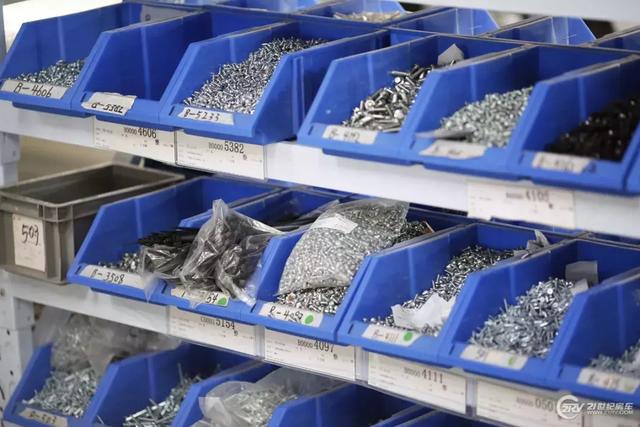
除了智能化,原厂品质还体现在每一个细节的严谨,上汽大通房车从设计到研发都遵循着科学严谨的态度,以乘用车标准制造房车,房车上小到一颗螺丝都有对应标准。
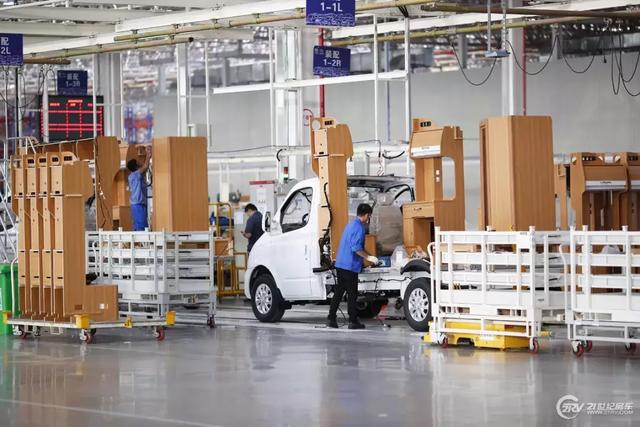
生产线上每一个工位都有对应的负责人,在完成本工位流程后,会对产品进行标准化自检。而当房车进入下一个工位时,下一工位的负责人也会在开始该工位流程前,对前一个工位的装配工作进行复检,通过两道检测保证装配工序不会出现错装漏装及装配不到位的现象,以严谨的态度铸就上汽大通房车的原厂品质。
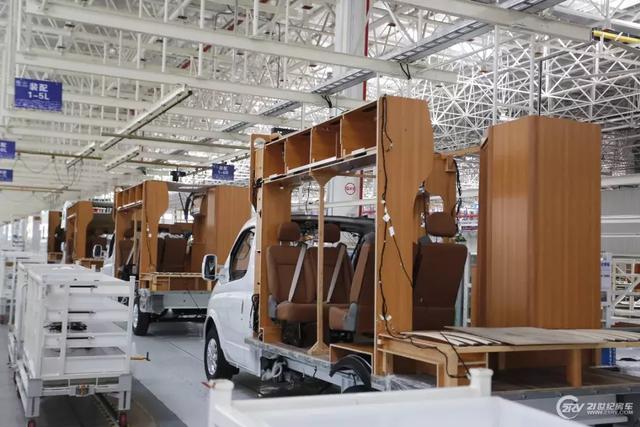
在生产线的5号工位我们已经能够看到上汽大通房车的雏形,至此房车内部的会客区、睡卧区及厨房区等已经逐渐成形,在随后的工位上工人将会对车内线束进行装配。
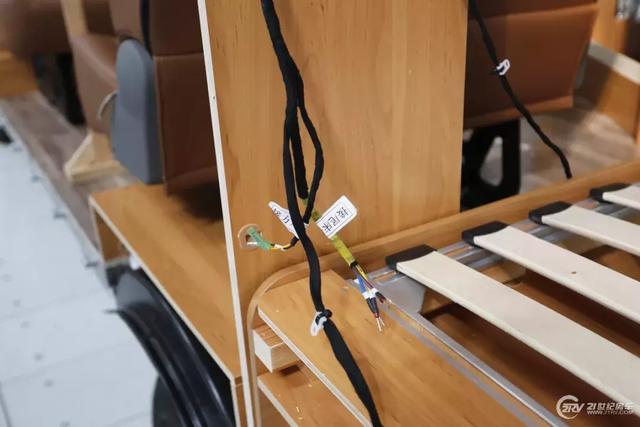
房车上所有线束均采用符合乘用车级别的整车线束,除了供应商的自检外,线束在进入工厂时也会再次进行检测,同时在每个线束上均带有清晰的功能标识,所有接插件的颜色及形状均有明确的定义从而加以区分。
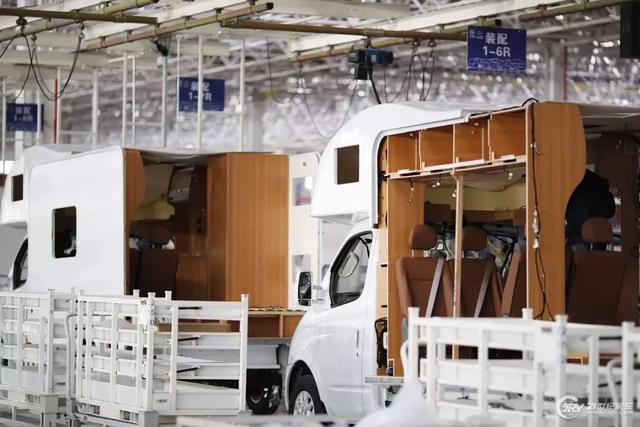
生产线的6、7、8三个工位主要为房车箱板及额头的合拼安装工位,对于C型房车来说也是重点环节,工厂内配备了吊具及高精度装配工具,来提高箱体安装精度,从而保证整车强度、密封性及耐用性。另外在房车选料方面,上汽大通房车科技公司的研发团队进行了大量的调研工作,由于国内房车单体车型产量不高,为了降低开发费用,对于额头、踏步及卫生间等普遍采用手糊玻璃钢产品,而手糊过程中使用的不饱和树脂会不停地释放苯类物质,严重影响室内空气质量。大通房车科技公司充分利用公司规模化优势,投入大量的工装模具,采用了真空导入、RTM、SMC

PUR-SRIM等新工艺,彻底的替代了手糊玻璃钢工艺,从而获得了良好的车内空气质量。
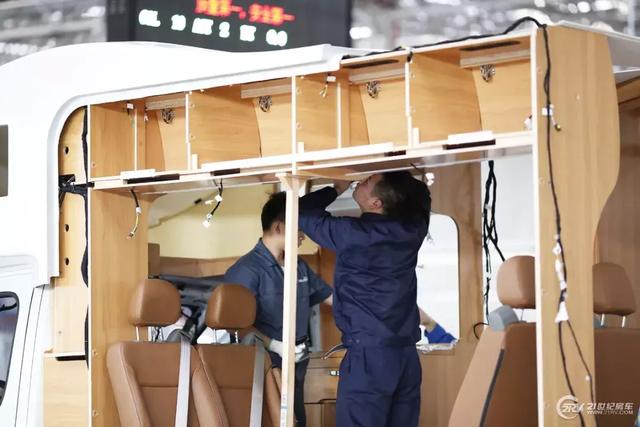
房车内顶大量运用了采用吸塑工艺制造的一体式模具件,从而减少车内的用胶量。另外吸塑件也采用了环保树脂,减少车内空气有害物质,大量模具件的使用也提高了整车的一致性和装配精度。
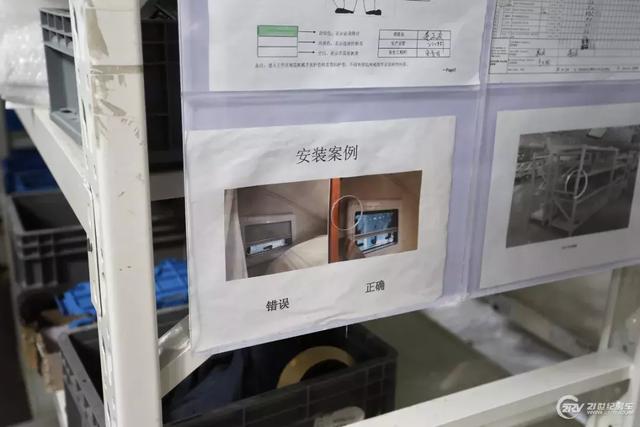
每个工位的装配工人在正式上岗前都会进行培训,通过2-3辆房车装配工作来熟悉流程,从而掌握装配工艺及操作要点,随后才会开始生产对外销售的房车;而用于培训的试装房车则会用来进行测试及静态展示,不会用于对外销售。
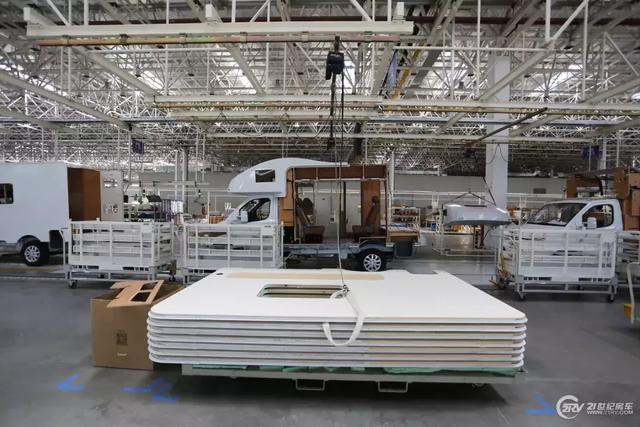
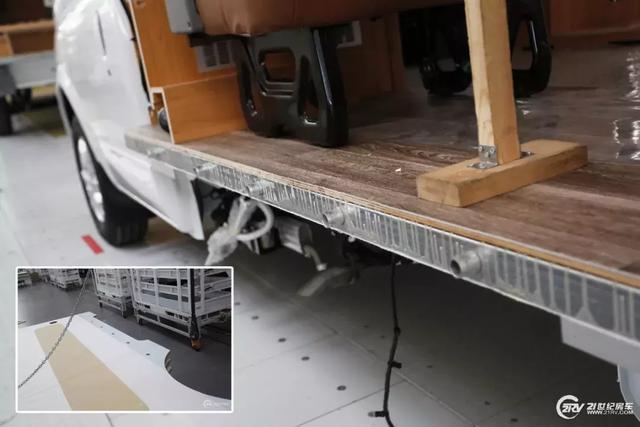
在传统的房车装配中,箱板的安装常通过尺量及划线方式进行定位,这种安装方式往往会存在不可避免的装配误差。而在上汽大通房车箱板及底板的合拼环节,上汽大通房车通过底板上的定位销及箱板上的定位孔来实现房车外观件的精准安装,箱板及底板通过机器开孔及焊接,具有更高的安装精度,从而保证产品质量的一致性。
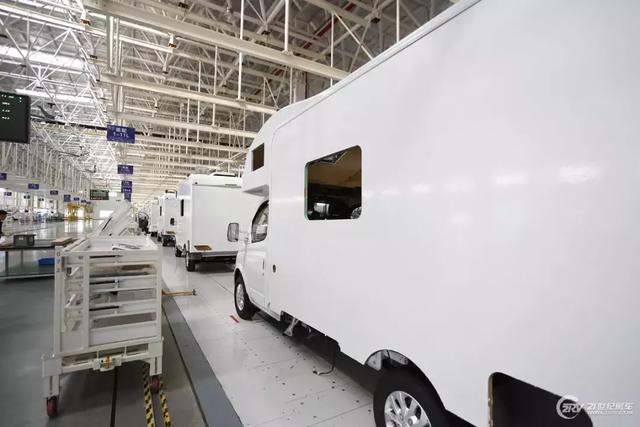
车厢制造区的厢板生产线一期采用负压设备,所压厢板表面光滑平整;二期将引进国际先进短周期热压机生产线,可实现分区加温,上下压板温差控制等先进的工艺,保证产品质量稳定可靠。

车身外部覆盖件也大量使用了吸塑件,在气味及重量方面相比玻璃钢材质都更有优势。
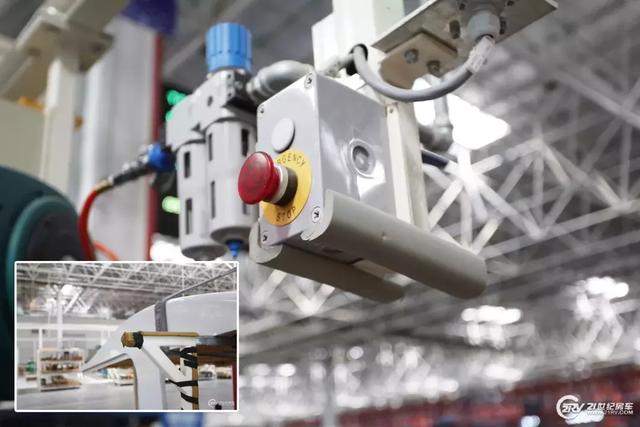
在参观溧阳房车生产基地时,我还发现了生产线上值得称赞的小细节,工位内一些比较突出的设备都会在边角包裹泡沫材料,从而避免工人意外受伤。
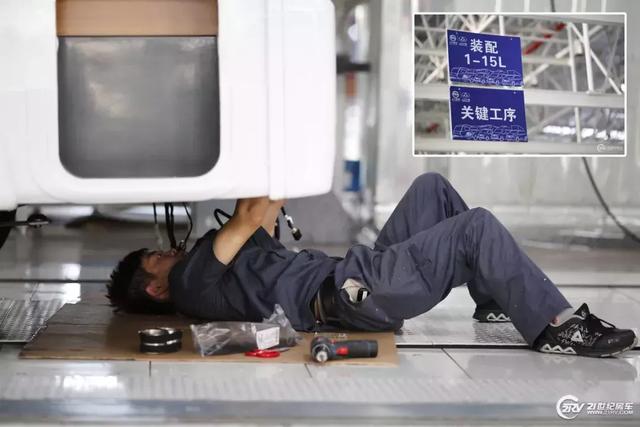
生产线上的某些工位还带有特别标识,据工作人员介绍, 一些关系到房车安全性及耐用性的装配流程都会被标记为关键工序,从而进行重点关注。
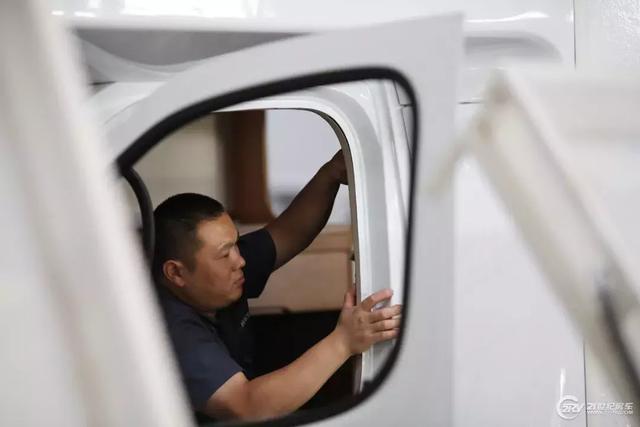
即使在装配完成后,工人也会对细节处进行自检,根据点检表进行标准化检测流程,以此确保产品质量的一致性。

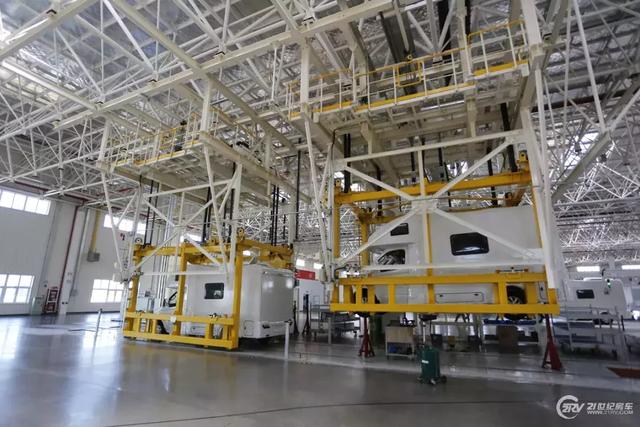
如前文所说,一条生产线共有21个工位,其中前面19个为地面工位,最后两个则为高工位,主要针对房车底盘处水箱及管路等进行连接及紧固。溧阳房车生产基地为提升生产效率及自动化程度,并区别于国内的传统房车制造工厂,在高工位参照整车厂生产模式,采用了自动化整体举升机。
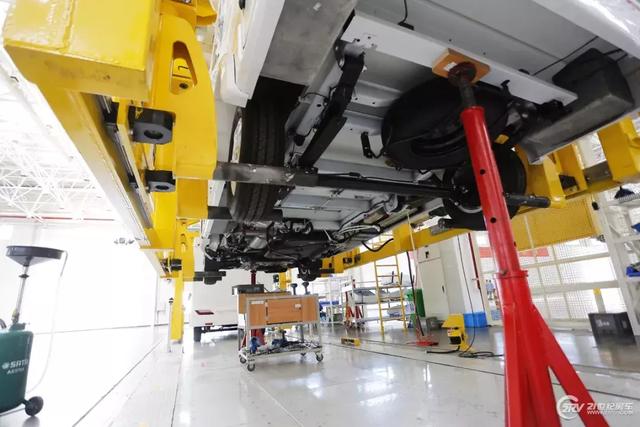
由于房车底部水箱及管路相对房车来说属于安全件,所以该工位安装工具也是采用在整车制造企业广泛应用的高精度工业级紧固工具,与民用紧固工具在精度上截然不同,小到一款螺丝需要上到多紧,都有相对应的标准。值得一提的是,上汽大通房车在底盘布置时,会进行大量的仿真计算,来验证车辆在发生碰撞时底盘的安全性。
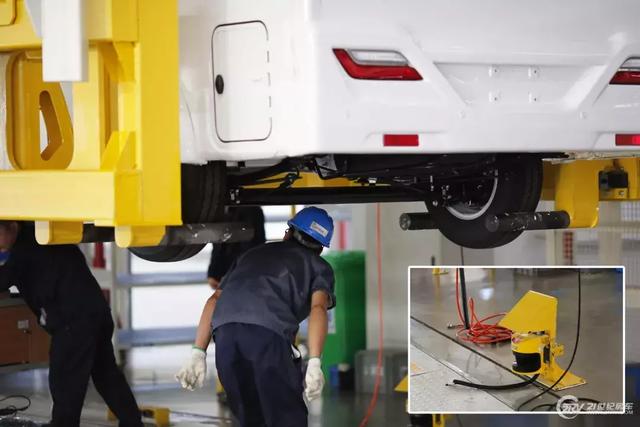
在高工位底部还配备有智能安全监测系统,当探测器监测到工位下方有工人正在进行工作时,举升机不会进行下降,从而保护工人安全,细节处体现工厂设计严谨。
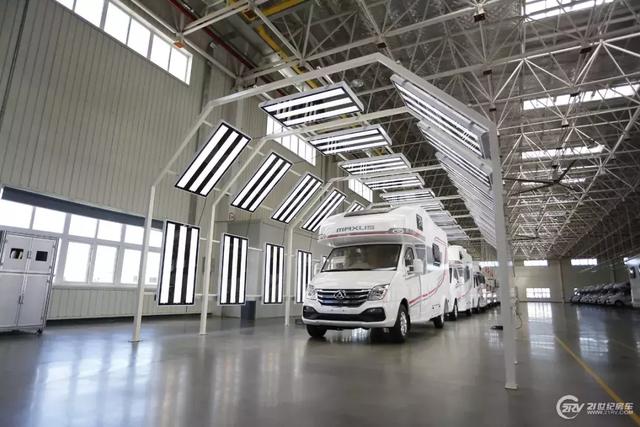
21个工位全部完成之后,房车还会进入房车质检工位,在光廊内对房车内外饰及功能进行最后的全面检查。值得一提的是,质检流程并非抽检而是全检,查出问题的房车会立即进行返修排除问题,从而保证从上汽大通溧阳房车生产基地下线的每一台房车都拥有可靠而统一的原厂品质。
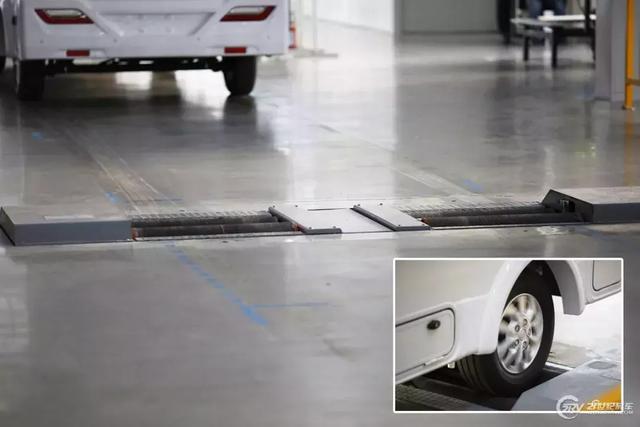
在进入光廊前,房车还会在制动力检测台上进行检测,以此保证房车的刹车系统正常工作。

整个光廊采用了乘用车检测标准,全方位覆盖的三色灯能够保证质检员更加细致地对房车外饰、装配、油漆质量及内饰进行检查。
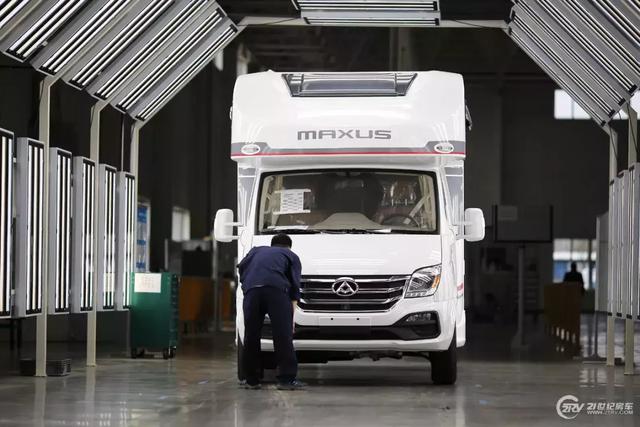
如质检员发现问题,会及时进行相应的返修工作。
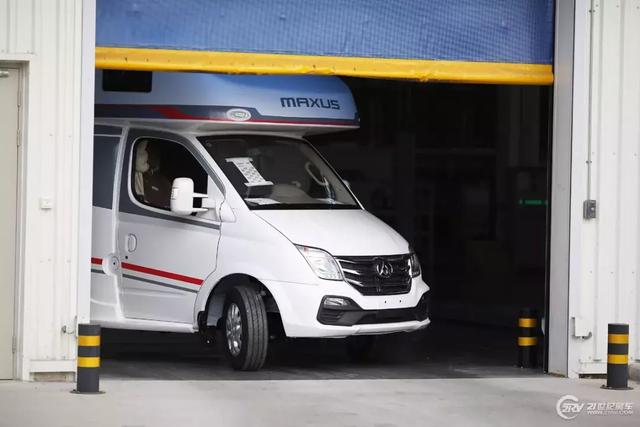
光廊检测完成后,房车会驶出工厂进入动态测试场地进行出场前的最后检测。
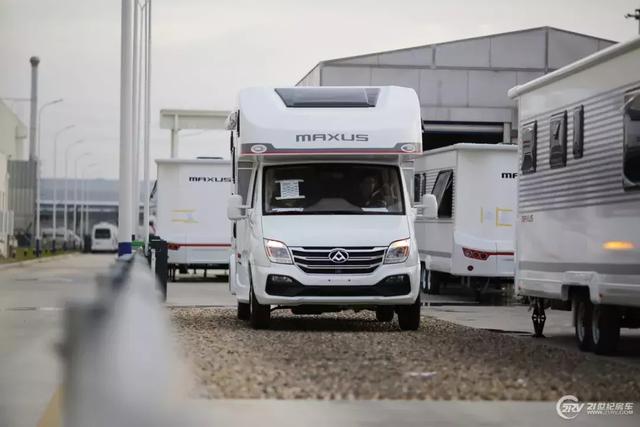
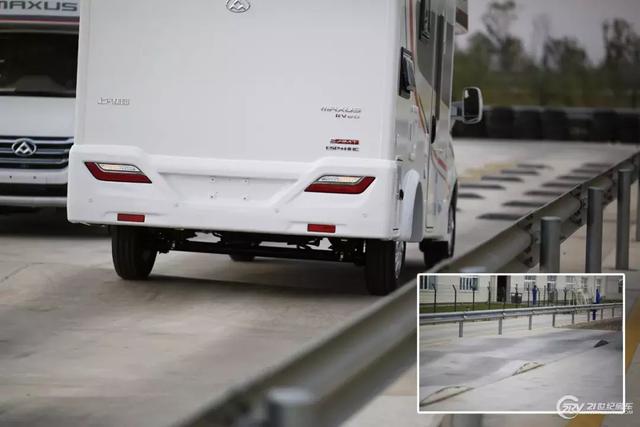
动态检测区域设有多个不同类型的坏路,用来模拟房车在日常行驶中可能遇到的各种路况,从而在房车出场前测试房车在颠簸路段的悬架滤震性能并排除由于底盘震动导致的车辆异响等问题。
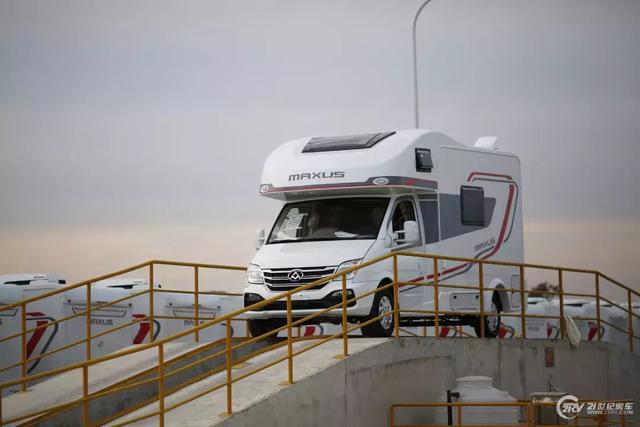
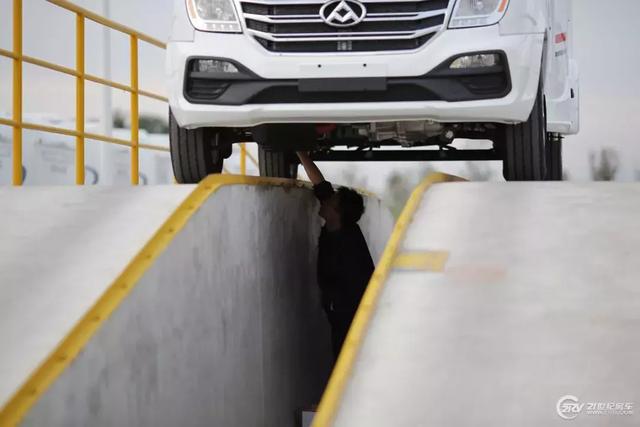
经过了坏路场地后,房车将驶上天沟并在坡顶驻车停留,随后工作人员将会下车对车辆底盘线路的密封性进行检测。
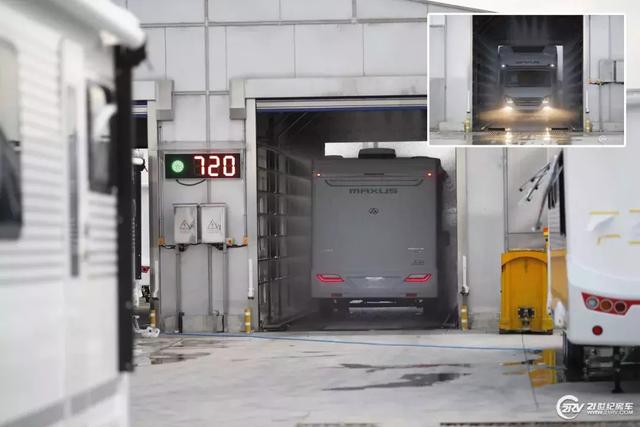
动态检测的最后环节为雨淋房测试,上汽大通房车将在雨淋房内进行720秒的整车淋雨测试。
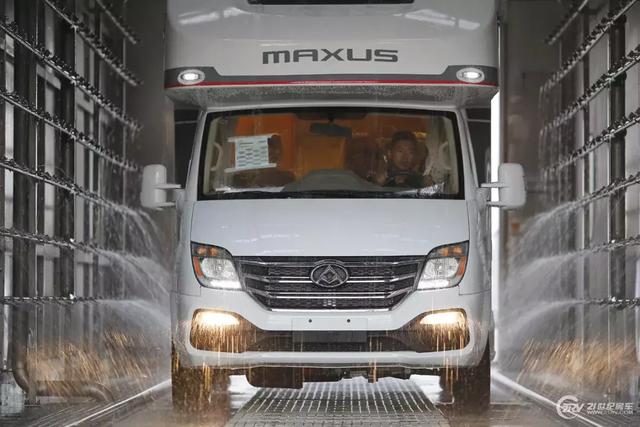
雨淋强度超过50年一遇的暴雨程度,从而测试房车在暴雨天气时的密封性,防止房车在使用中出现漏水现象,并测试房车外部照明及信号装置密封性。
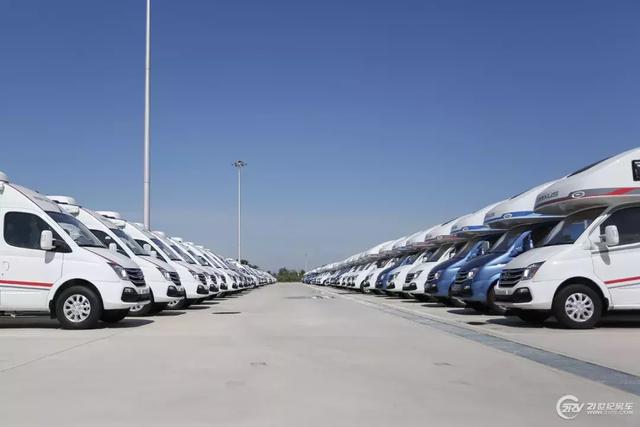
经过一系列动态检测后,整个质检环节完毕,上汽大通房车将驶入停车场等待交付客户。
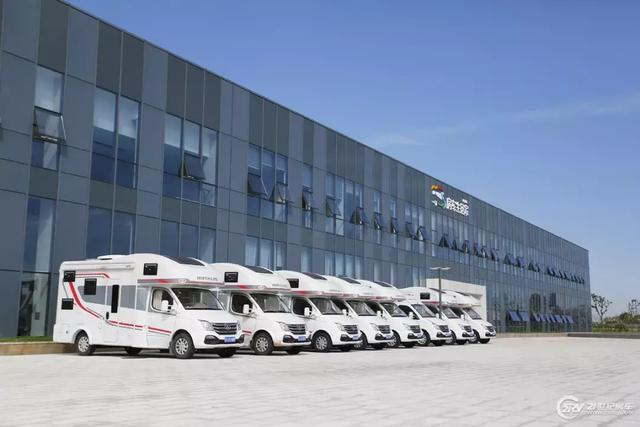
在上汽大通溧阳房车生产基地内还有着展示中心及多功能区域,主要用于车辆展示及研发人员办公。
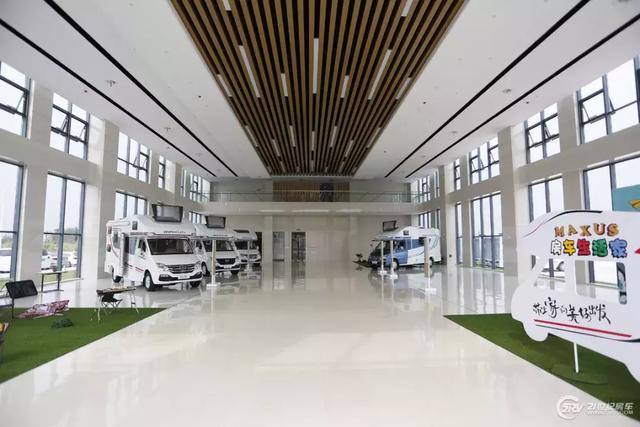
在展示中心内布置有展厅,内部陈列有上汽大通房车旗下最新产品。
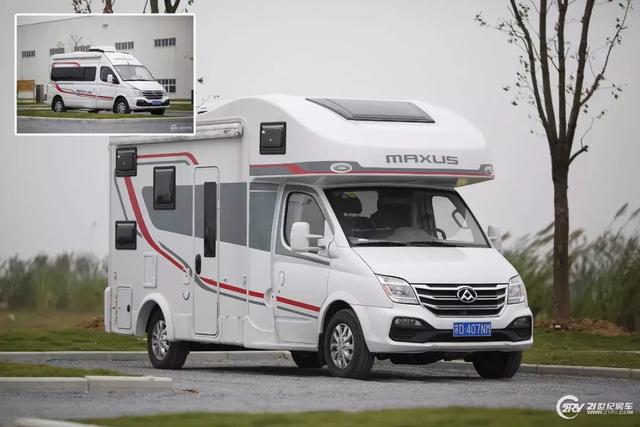
在展示中心后方还有房车生态体验区,体验区内停放有包括自行式C型、B型及拖挂式多种上汽大通旗下房车,并配套有诸如水电桩等完善的房车营地设施,为客户提供接触了解房车的机会。
总结:上汽大通溧阳房车生产基地是目前当之无愧的中国最大的房车生产基地,颠覆了传统房车制造行业“于底盘上改装”的房车生产模式,而是遵循整车开发标准流程的正向设计,有着规范化的造型设计、结构设计、虚拟分析及实验认证的完整流程,将房车设计生产模式从“小作坊”形式提升到“乘用车标准”。上汽大通溧阳房车生产基地实现了自动流水线生产,配备可视化操作信息系统,实时显示车辆装配要求,配合SPS物流系统和分拣系统,采用行业领先的AGV/AGC自动托运,最大程度实现智能化和效率化。整个制造流程中通过智能排产系统,绑定客户定制订单,实现了C2B定制及全程质量监控及追溯。上汽大通将房车做为一个整车的研发思路充分考虑了房车的安全性、环保性、整体性和易维修性。同时基于原有整车的生产经验,将制造汽车的标准和技术引入并应用在房车生产之上,尽可能多的让房车制造标准化和自动化,使得从上汽大通溧阳房车生产基地下线的每一台房车都拥有完全一致的可靠质量,这也是上汽大通原厂品质的关键所在。
电脑